Prozessprüfbares Thermometersystem (Redaktioneller Beitrag in der Deutschen Molkereizeitung)
Abstract: Das von der Fa. tmg neu entwickelte prozessprüfbare Thermometersystem wurde im Rahmen einer Typprüfung nach den Richtlinien des Erhitzerausschusses für die Anwendung in Milcherhitzungsanlagen begutachtet.
Das prozessprüfbare Thermometersystem bietet eine Möglichkeit, die gemessene Erhitzungstemperatur von Milch oder von anderen Medien im Nahrungsmittelbereich während des Prozesses mit höherer Genauigkeit und geringerem Aufwand zu überprüfen. Damit trägt es wesentlich zu einer sicheren Wärmebehandlung, insbesondere bei der Pasteurisierung von Milch, bei und erfüllt die Eigenschaft einer Referenzmessstelle.
Für Anwendungen in der Pharmazie oder in der Medizintechnik ist das System ebenfalls sehr gut geeignet.
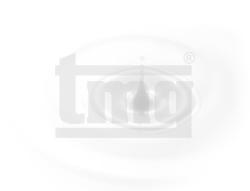
Dr. Ing. Christian Kiesner, Dipl. Ing. Sönke Matzen, Max Rubner-Institut, Bundesforschungsinstitut für Ernährung und Lebensmittel, Institut für Sicherheit und Qualität bei Milch und Fisch, Kiel
Es wird ein neues Thermometersystem für den Einsatz in Milcherhitzungsanlagen vorgestellt, das die gemessene Erhitzungstemperatur während des Prozesses mit höherer Genauigkeit und geringerem Aufwand überprüft.
Im Rahmen einer Typprüfung nach den Richtlinien des Erhitzerausschusses wurde ein prozessprüfbares Thermometersystem für die Anwendung in Milcherhitzungsanlagen begutachtet. Die Bezeichnung „prozessprüfbar“ steht für die Möglichkeit, einen Temperaturfühler im laufenden Prozess, ohne Ausbau, durch eine Referenzmessung überprüfen zu können. Es stellt somit eine Kombination von Temperaturfühler und Referenzmessstelle dar. Als Referenzmessung wird in der Messtechnik die Bestimmung der systematischen Fehler einer Messmethode bezeichnet, die durch Vergleichsmessung mit einem Instrument übergeordneter Genauigkeit erfolgt. Die Forderung nach einer Referenzmessstelle wird in der Regel erhoben, wenn es sich um technologische Prozesse handelt, deren Temperatur nah an einem festgelegten Grenzwert liegt. Dies ist insbesondere bei der Kurzzeiterhitzung (Pasteurisierung) von Rohmilch der Fall. Neben der gewünschten schonenden Wärmebehandlung der Milch müssen gleichzeitig untere Grenzwerte, die formell festgelegt sind (mind. 72 °C / mind. 15 Sekunden), stets eingehalten werden. Die Einhaltung dieser unteren Grenzwerte sorgt für den Schutz des Verbrauchers vor mikrobiellen Risiken. Anlagentechnisch muss dafür ein geeignetes, validierbares Überwachungssystem unter Zuhilfenahme von Grenzwerten den Prozess kontinuierlich überwachen (Monitoring).
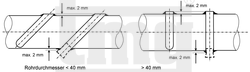
Bislang wird die Kontrolle der relevanten, im Prozess verwendeten Temperaturfühler (Prozessfühler) durch die in regelmäßigen Zeitabständen durchgeführten Abgleichsmessungen mit einem kalibrierten Messfühler durchgeführt (Verifizierung). Dafür muss der Prozessfühler aus der Milcherhitzungsanlage ausgebaut werden. Eine weitere Möglichkeit der Abgleichsmessung ohne Ausbau des Prozessfühlers ist der Einbau von Messhülsen in dessen unmittelbarer Nähe. Beispiele für den Einbau solcher Messhülsen sind in der Richtlinie „Mess-, Regel-, Kontroll- und Sicherheitseinrichtungen für Milcherhitzungsanlagen“ aufgeführt (Abb.1). Der Einbau von Messhülsen in den Milchleitungen einer Milcherhitzungsanlage war bislang die einzige Möglichkeit, die Messgenauigkeit des Prozessfühlers bzw. der Messkette während des laufenden Prozesses mithilfe eines geeichten Glasthermometers zu prüfen. Da die Messung jedoch nicht am selben Ort und nicht mit Fühlern der gleichen thermischen Massen erfolgt, treten mehr oder weniger große Abweichungen der Messwerte auf. Zusätzlich verengen die Messhülsen den Strömungsquerschnitt und stellen weiterhin eine Fläche für die Bildung von Milchbelag (Foulingschicht) dar. Reinigungstechnisch ist diese Lösung eher negativ zu bewerten.
Die Firma tmg Temperaturmesstechnik Geraberg GmbH in Martinroda hat ein prozessprüfbares Thermometersystem entwickelt, bei dem die erwähnten Nachteile des Messhülsensystems abgestellt werden. Das prozessprüfbare Thermometersystem stellt eine Kombination aus einem Temperaturfühler und einer messortsgleichen Referenzmessstelle dar. Der Temperaturfühler ist mit einem zusätzlichen Prüfrohr ausgerüstet, in das ein kalibrierter Prüffühler (Referenzfühler I) eingeführt wird, der die Temperatur am gleichen Ort wie der Temperaturfühler messen kann. Das Prinzip des Prüffühlers in den verschiedenen Ausführungen des prozessprüfbaren Thermometersystems ist in Abb. 2 dargestellt.
Nach dem Öffnen des Deckels auf dem Anschlusskopf kann über die Revisionsöffnung ein kalibrierter Prüffühler (ø 1,6 mm) eingeführt werden. Dieser ermöglicht eine Überprüfung des Temperaturfühlers mit der angeschlossenen Messkette ohne Ausbau am Messpunkt. Der Prüffühler erfasst also die Temperatur nahezu an der gleichen Position wie der zu überprüfende Temperaturfühler.
Begutachtung des Thermometersystems
Für die Begutachtung des prozessüberprüfbaren Thermometersystems wurden vier verschiedene Fühler mit Prüfröhrchen und zwei Prüffühler mit unterschiedlichen Längen herangezogen. Die Fühler trugen die Kennung des Herstellers WÜ84.5-ppr-328 mit Clamp-ISO-Flansch, WÜ82.2-ppr-328 mit Überwurfmutter auf Silikon-Quetschkonus, WÜ88.5-ppr-328 mit Kegelstutzen nach DIN 11851 und WH51.0-ppr-228 mit Gewinde G1/2A für Behältereinsatz. Als Prüffühler wurden die Fühler mit Kennung WQ0340-0012 verwendet. Neben einer Überprüfung der Genauigkeit der Temperaturfühler im Wasserbad wurden weitere Versuche in einer mit Wasser durchströmten Rohrleitung DN 40 durchgeführt.
In der Rohrleitung wurden eingebaut: (Abb. 3)
- ein durch Silikonstopfen direkt in die Leitung eingestochenes Einstechschutzrohr für den Referenzfühler I,
- eine Messhülse, wie in Abb. 1 dargestellt, für den Referenzfühler II
- ein prozessprüfbarer Temperaturfühler.
Als Referenzfühler II wurde ein kalibrierter Pt-100 Sensor mit einem Durchmesser von 3 mm verwendet und an ein Handanzeigegerät angeschlossen. Die Eintauchtiefe des Fühlers in der mit Silikonöl befüllten Messhülse betrug 45 mm. Damit lag sie etwa beim 15-Fachen des Fühlerdurchmessers und entspricht somit den Anforderungen an eine gute Laborpraxis. Die Strömungsgeschwindigkeit des Wassers in der Rohrleitung lag bei 1 m/s und die Temperaturen wurden zwischen +40°C bis +145°C variiert. An den Temperaturpunkten +72°C, +90°C und +135°C wurden in wiederholten Versuchen die gemessenen Werte miteinander verglichen. Dabei wurde der Referenzfühler I in jedem Temperaturbereich für jeweils mindestens zehn Minuten in den prozessprüfbaren Temperaturfühler sowie in das Einstechschutzrohr eingeführt. Wie die Messergebnisse in Tab. 1 zeigen, kommt es bei dem Referenzfühler II trotz ausreichender Eintauchtiefe zu einem systematischen Messfehler. Fehlerquellen können z. B. Abstrahlverluste sein, da das Prinzip der Messhülsen auf der Messung mit Glasthermometern basiert. Die Messwerte des prozessprüfbaren Temperaturfühlers und des Referenzfühlers I wichen um maximal 0,16 K voneinander ab. Die Messabweichungen zwischen den Referenzfühlern I und II steigen mit zunehmender Temperatur. Diese Abweichung bewegt sich am äußersten Rand der Toleranzen und ist im Grunde nicht mehr zeitgemäß. Mit dem prozessprüfbaren Thermometersystem ist eine schnelle, einfache und genaue Überprüfung der gesamten Messkette möglich. Die Messunsicherheit ist wesentlich geringer als bei der bisher verwendeten Messhülse.
Zusammenfassung
Zusammenfassend kann festgestellt werden, dass das vorgestellte prozessprüfbare Thermometersystem eine Möglichkeit bietet, die gemessene Erhitzungstemperatur von Milch oder von anderen Medien im Nahrungsmittelbereich während des Prozesses mit höherer Genauigkeit und geringerem Aufwand zu überprüfen. Damit trägt es wesentlich zu einer sicheren Wärmebehandlung, insbesondere bei der Pasteurisierung von Milch, bei und erfüllt die Eigenschaft einer Referenzmessstelle.1
Eine weitere Anwendung des Systems in der Pharmazie oder in der Medizintechnik wäre ebenso vorstellbar.
1 Bericht Nr. M 23/10 – Prüfkennzeichen: KI-M 23/10 – Pkt 5/S.6
Tab. 1: Zusammenstellung der Messergebnisse aus dem Vergleich der Temperaturen in der Rohrstrecke
Temperatur in [°C] | Messabweichung in [K] | |
Referenzfühler I - Referenzfühler II | ppr Temperaturfühler - Referenzfühler I | |
72 | -0,5 | -0,02 |
90 | -0,8 | -0,05 |
135 | -1,8 | -0,16 |